Bezpieczeństwo energetyczne hal przemysłowych – jak uniknąć przerw w dostawie energii?
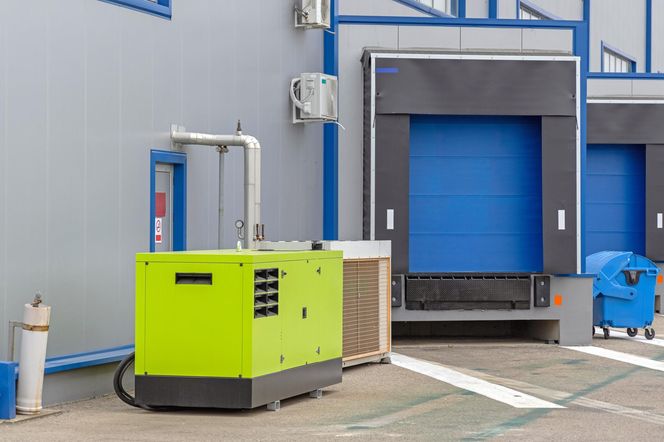
Przerwy w dostawie prądu mogą spowodować starty finansowe i wizerunkowe przedsiębiorstwa. Z uwagi na to konieczne staje się wyposażenie hal produkcyjnych w systemy zapewniające bezpieczeństwo energetyczne. Istotną rolę odgrywają tu również audyty, przeglądy i serwisy, które ograniczają ryzyko powstania awarii zasilania.
Spis treści
- Jakie skutki powodują przerwy w dostawie prądu?
- Bezpieczeństwo energetyczne w halach – system zasilania awaryjnego
- Przerwy w dostawie prądu a OZE i akumulatorowe magazyny energii
- Bezpieczeństwo energetyczne – systemy zarządzania energią (EMS)
- Audyty, przeglądy i serwisy – redukcja ryzyka awarii zasilania
Coraz większa automatyzacja produkcji, realizowanie napiętych harmonogramów produkcyjnych czy wykonywanie bardzo precyzyjnych procesów z wykorzystaniem kosztownych materiałów prowadzi do tego, że nawet krótkie przerwy w dostawie prądu narażają przedsiębiorstwo produkcyjne na spore straty. I to bez względu na to, czy wina leży po stronie sieci energetycznej, niesprzyjających warunków atmosferycznych, awarii sprzętu czy też błędu pracownika lub w zarządzaniu. Żeby ograniczyć potencjalne straty, należy więc zapewnić bezpieczeństwo energetyczne poprzez niezawodność dostaw energii. Wszelkie rozwiązania z tego obszaru są dziś równie ważnym czynnikiem zwiększania wydajności i utrzymania konkurencyjności przedsiębiorstwa, jak maszyny i urządzenia produkcyjne czy dobrze zaplanowany proces produkcyjny.
Jakie skutki powodują przerwy w dostawie prądu?
Każdy nieplanowany przestój w produkcji to dla przedsiębiorstwa przemysłowego przede wszystkim określone straty finansowe. W przypadku firm, które produkują duże partie towarów, przerwy w dostawie prądu oznaczają realny spadek produkcji, którego nie da się już nadrobić, a w konsekwencji mniejszą sprzedaż. Przestój w produkcji to z kolei możliwe opóźnienie w realizacji zamówienia, z czym mogą się wiązać także kary umowne. W przypadku przerwy w dostawie prądu w trakcie realizacji procesu produkcyjnego może się okazać, że wykorzystywane w nim surowce czy różnego rodzaju podzespoły nie będą już nadawać się do ponownego użycia. Nagła przerwa w procesie technologicznym może ponadto wymagać czasochłonnego przywrócenia możliwości wznowienia produkcji. Konieczna może być np. ponowna kalibracja maszyn czy też usunięcie z linii produkcyjnej uszkodzonych półproduktów. Z kolei brak zasilania w systemach wentylacyjnych, ogrzewania lub chłodniczych – np. w branży chemicznej, spożywczej czy każdej innej, która wymaga specyficznych warunków środowiskowych – stwarza dodatkowe ryzyko, że realizowane procesy będą nieprawidłowe, a przechowywane produkty będą niezdatne do użytku.
Jednak przestoje produkcyjne mogą oznaczać dla przedsiębiorstwa również straty wizerunkowe i utratę reputacji, które pośrednio będą wpływać na finanse firmy. Opóźnienia w dostawie czy niezrealizowanie zamówienia będą się wiązać z niezadowoleniem klienta, a nawet jego utratą, zwłaszcza jeśli niezawodność dostawy była kluczowa w danym zamówieniu.
Straty finansowe i wizerunkowe mogą wynikać również z gorszej jakości wytworzonych produktów. Przerwa w dostawie prądu, zwłaszcza w kluczowym momencie procesu produkcyjnego, który wymaga dużej precyzji i powtarzalności, może prowadzić do problemów z utrzymaniem zakładanej jakości. Może się okazać, że nawet krótkotrwała przerwa sprawi, iż finalny produkt nie spełni zakładanych norm jakościowych i nie przejdzie kontroli jakości. W konsekwencji konieczne będzie ponowne wykonanie tego samego procesu, co może wpływać na opóźnienie realizacji zamówienia i zwiększenie ilości odpadów.
Nagłe przerwy w dostawie prądu mogą także powodować zagrożenia zarówno dla zdrowia i życia pracowników, jak i dla maszyn czy urządzeń produkcyjnych. Brak prądu to m.in. brak oświetlenia czy nieprawidłowe funkcjonowanie systemów bezpieczeństwa. Ponadto nagłe wyłączenie urządzeń może prowadzić do ich awarii lub długotrwałego ich ponownego uruchomienia. W wyniku braku energii elektrycznej mogą przestać działać również systemy alarmowe czy monitorujące, co może opóźnić właściwą reakcję na zagrożenie.
Bezpieczeństwo energetyczne w halach – system zasilania awaryjnego
Do najczęściej stosowanych środków zaradczych, które mają zminimalizować ryzyko i potencjalne straty, które spowodowane są przez przerwy w dostawie prądu, należą systemy zasilania awaryjnego, które zapewniają przez pewien czas ciągłość działalności operacyjnej przedsiębiorstwa. Ich zadaniem jest dostarczanie energii elektrycznej w przypadku awarii głównego zasilania. W ramach tej grupy rozwiązań można wyróżnić kilka rodzajów systemów.
W zastosowaniach przemysłowych (choć nie tylko) funkcję ochrony przed nagłymi zanikami zasilania czy innymi zakłóceniami w sieci elektroenergetycznej pełnią przeważnie zasilacze UPS (Uninterruptible Power Supply), które zapewniają natychmiastowe zasilanie w przypadku przerwy w dostawie prądu. Stosuje się je zwłaszcza w celu ochrony krytycznych urządzeń i systemów, w przypadku których niezawodne zasilanie jest koniecznością. Mogą one zapewniać ochronę centralną (jeden UPS chroni np. wszystkie urządzenia pracujące w hali przemysłowej), jak i indywidualną (każde urządzenie ma swój własny zasilacz UPS). Wśród zasilaczy UPS wyróżniamy zasilacze offline, line-interactive i online. Zasilacze offline zapewniają podstawową ochronę tylko przed krótkimi zanikami prądu (nie chronią już jednak przed przepięciami czy wahaniami napięcia). UPS line-interactive to urządzenie, które dodatkowo automatycznie reguluje dostarczane napięcie. Najbardziej zaawansowanym rozwiązaniem są obecnie zasilacze online, które chronią przed większością zakłóceń i dzięki temu zapewniają nie tylko niezawodne, ale również stabilne zasilanie.
Rolę systemów zasilania awaryjnego mogą pełnić również agregaty prądotwórcze. Ich największa zaleta to możliwość generowania energii przez dłuższy czas, co jest szczególnie istotne podczas poważnej awarii, gdy przerwa w dostawie prądu może potrwać dłużej. Również w przypadku agregatów prądotwórczych występują różne rodzaje tych urządzeń. Najbardziej pożądane są warianty z układem automatycznego rozruchu, które samoczynnie się uruchamiają po wykryciu braku zasilania, co minimalizuje czas przestoju sprzętu.
Połączenie zasilacza UPS z agregatem prądotwórczym jest rozwiązaniem, które zapewnia bardziej kompleksową ochronę. Zasilacz UPS gwarantuje natychmiastowe zasilanie w przypadku nagłej przerwy w dostawie prądu, a agregat jest w stanie zapewnić ciągłość zasilania przez dłuższy czas.
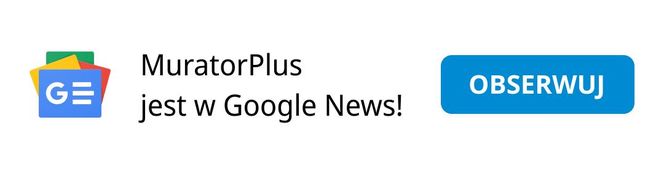
Przerwy w dostawie prądu a OZE i akumulatorowe magazyny energii
W ostatnim czasie na popularności zyskują instalacje fotowoltaiczne i wiatrowe, dzięki którym również przedsiębiorstwa przemysłowe mogą zmniejszyć swoje obciążenia finansowe związane z zużyciem energii elektrycznej. Co istotne, odnawialne źródła energii mogą stanowić także swego rodzaju zabezpieczenie przed przerwami w dostawach prądu z sieci energetycznej. Kluczową rolę w tym kontekście odgrywają jednak magazyny energii, które standardowo służą do gromadzenia nadwyżki wyprodukowanej ze słońca lub wiatru energii (gdy zużycie energii jest mniejsze niż jej produkcja) i wykorzystywanej, gdy zużycie prądu wzrasta.
Te same magazyny, a dokładniej zgromadzona w nich energia elektryczna, mogą służyć jako zabezpieczenie przed chwilowymi przerwami w dostawach prądu z sieci energetycznej. Rozwiązanie to ma jednak pewne wady, gdyż może służyć jako zasilanie awaryjne jedynie w sytuacji, gdy w akumulatorach znajduje się dość dużo zgromadzonej energii. Po okresie, w którym nie była ona wytwarzana lub produkcja była niewielka (np. po nocy lub pochmurnym dniu) może okazać się, że magazyny energii nie będą w stanie zapewnić dostatecznej jej ilości.
Bezpieczeństwo energetyczne – systemy zarządzania energią (EMS)
Bardzo ważnym elementem w kontekście zapobiegania przerwom w dostawie energii są systemy zarządzania energią. Dzięki nim przedsiębiorcy na bieżąco monitorują zużycie energii w całym przedsiębiorstwie i w poszczególnych jego obszarach. Pozwala to szybko zidentyfikować wszelkie nieprawidłowości, dzięki czemu można odpowiednio wcześnie zaplanować działania naprawcze. Co więcej, inteligentne systemy zarządzania energią w przedsiębiorstwie, na podstawie danych bieżących i historycznych, są w stanie nawet przewidzieć, gdzie może dojść do problemów z zasilaniem.
Ważna jest również integracja systemów EMS z systemami zarządzania produkcją, zarządzania magazynem, zarządzania systemami HVAC (ogrzewania, wentylacji i klimatyzacji) i innymi, co pozwoli zoptymalizować zużycie energii przez poszczególne obszary przedsiębiorstwa. Dzięki takiemu współdziałaniu różnych systemów możliwe jest automatyczne reagowanie w czasie rzeczywistym na zmieniające się warunki (np. wyłączanie nieaktywnych urządzeń, optymalizowanie pracy maszyn produkcyjnych, regulowanie temperatury). Może pomóc to w zmniejszeniu zużycia energii, ale również odgrywa kluczową rolę w sytuacji szczytowego zapotrzebowania na energię i efektywnego wykorzystania jej magazynów.
Audyty, przeglądy i serwisy – redukcja ryzyka awarii zasilania
Na bezpieczeństwo energetyczne wpływa również regularne kontrolowanie jakości instalacji. W tym celu należy przeprowadzać audyty energetyczne oraz przeglądy całej sieci i jej poszczególnych elementów, w tym maszyn i urządzeń, które są odbiorcami energii elektrycznej w zakładzie produkcyjnym. Wykonywane okresowo czynności serwisowo-konserwacyjne i modernizacja (lub wymiana) przestarzałego sprzętu pozwalają utrzymywać całą instalację w dobrym stanie przez dłuższy czas. I choć nie są gwarantem, że nie dojdzie do awarii zasilania, to przynajmniej w dużym stopniu zredukują takie ryzyko.
Ponieważ nie da się całkowicie wyeliminować ryzyka przerw w dostawie prądu, ważne jest również opracowanie odpowiedniego planu działania w takiej sytuacji. Odpowiedni zespół pracowników powinien jak najszybciej podjąć określone działania zgodnie z procedurami. Pozostali pracownicy również powinni zostać przeszkoleni, jak się zachowywać w takich przypadkach. Jest to kluczowe, żeby jak najszybciej przywrócić możliwości operacyjne przedsiębiorstwa, a jednocześnie nie powiększać negatywnych skutków niespodziewanej przerwy w dostawie energii.
- Zobacz też: Największe hale przemysłowe powstające w Polsce
Autor: Panattoni
Panattoni Park Będzin – 89 tys. m2