Podstawowa funkcja materiałów izolacyjnych pozostaje bez zmian – muszą one zapewnić odpowiednie parametry fizykalne przegród budowlanych. W pierwszej kolejności zwraca się uwagę na współczynnik przewodzenia ciepła λ, który określa właściwości cieplne materiałów. Im jego wartość jest niższa, tym właściwości materiału lepsze, a straty ciepła przez przegrody mniejsze. Na rynku dostępne są materiały izolacyjne o współczynniku λ na poziomie 0,019–0,045 W/(mK). Przed wyborem konkretnego materiału termoizolacyjnego należy ponadto zapoznać się z następującymi cechami:
- gęstość objętościowa,
- izolacyjność akustyczna,
- przepuszczalność pary wodnej,
- współczynnik oporu dyfuzyjnego μ,
- wrażliwość na czynniki biologiczne i chemiczne,
- odporność ogniowa,
- informacja o jego zastosowaniu.
Przegląd materiałów izolacyjnych
Najczęściej stosowany materiał izolacyjny – EPS
Jest to produkt powstający w procesie przetwarzania ropy naftowej albo neoporu, które zmieniają się w styren, a następnie, po wymieszaniu z wodą i gazem porotwórczym, w polistyren – twardy, szklisty granulat. Pod wpływem podgrzania znajdujący się w nim czysty wodór rozpręża się i granulki wielokrotnie zwiększają swoją objętość. Po wymaganym sezonowaniu i napowietrzaniu stają się sprężyste i odporne na ściskanie, a miejsce wodoru, na skutek przetwarzania technologicznego, zajmuje w nich powietrze. Polistyren EPS (popularnie zwany styropianem) powstaje w wyniku ekspandowania granulatu, czyli spieniania go przy użyciu pary wodnej. To najczęściej stosowany materiał izolacyjny. Dostępny jest w kilku odmianach, w zależności od zastosowania: fasadowy, podłogowy, fundamentowy oraz do izolacji termicznej poddaszy i dachów.
Styropian nie jest odporny na rozpuszczalniki organiczne (m.in. aceton, benzol, nitro, terpentynę), bitumy, produkty smołowe, benzynę, a przy dłuższym kontakcie także na oleje, dlatego nie powinien być używany w miejscach, w których byłby narażony na kontakt z nimi lub z ich oparami. Najpopularniejszy wymiar płyty styropianowej to (dł./szer.) 50/100 cm, a ich grubość może wynosić od 10 aż do 1200 mm. Krawędzie mogą być proste, do łączenia na zakład lub na pióro-wpust. Współczynnik przewodzenia ciepła λ mieści się w przedziale od 0,031 do 0,044 W/(mK). Do innych najważniejszych parametrów określających właściwości EPS należy zaliczyć:
- wytrzymałość na rozciąganie prostopadle do powierzchni czołowych (TR) − wskazuje odporność na rozerwanie we własnej strukturze, odgrywa istotną rolę w ociepleniu elewacji. Norma PN-EN 13163 określa siedem poziomów tego parametru: TR20, TR50, TR80, TR100, TR150, TR200, TR400, w którym część liczbowa przedstawia minimalną wartość obciążenia rozciągającego w kPa. Do zastosowania na fasadzie należy wybierać produkty TR100 lub 80 kPa (tylko w przypadku potwierdzenia odpowiednimi certyfikatami bądź rekomendacjami niezależnego instytutu badawczego);
- naprężenia ściskające przy 10-procentowym odkształceniu (CS) − jest to stosunek siły ściskającej do powierzchni płyty styropianowej przy 10-procentowym odkształceniu. Liczba 10 oznacza odkształcenie, pozostałe (jest 15 poziomów) podają natomiast minimalną wartość naprężenia ściskającego wyrażonego w kPa. Parametr ten jest istotny w przypadku zastosowania w konstrukcjach przenoszących obciążenia, np. do izolacji termicznej podłóg lub dachu, i wpływa na twardość oraz odporność ocieplenia.
Zadeklarowane przez producenta parametry powinny być umieszczone na etykiecie na opakowaniu płyt styropianowych.
Rodzaje płyt styropianowych
Można wyróżnić trzy podstawowe rodzaju styropianu: biały, biały w szare kropki oraz grafitowy. Styropian grafitowy charakteryzuje się najlepszym współczynnikiem przewodzenia ciepła –λd ≤ 0,030 W/(mK), uzyskanym dzięki odpowiedniej kompozycji surowców, do których dodawany jest np. grafit. Często określa się go jako styropian drugiej generacji, stosuje się go w budownictwie energooszczędnym i pasywnym. Trzeba jednak pamiętać, że montaż jest bardziej wymagający, należy więc bezwzględnie przestrzegać wymogów zawartych w instrukcji, w przeciwnym razie na skutek silnych naprężeń wewnętrznych mogą się one odkształcać pod wpływem zmian temperatury (dzień/noc) lub bezpośredniego działania promieni słonecznych. Może to prowadzić do powstawania mostków cieplnych, a nawet odpadania płyt od fasady.
Mając na uwadze pojawiające się problemy, producenci udoskonalili technologię produkcji, w wyniku czego na rynku pojawiła się kolejna – trzecia – generacja styropianu, produkowana w technologii odprężonych płyt zespolonych. Dzięki kilkumilimetrowej ochronnej, białej warstwie styropianu (lub białej farbie refleksyjnej) zespolonej z grafitowym rdzeniem płyty są odporne na działanie słońca nawet po szlifowaniu. Ponadto fabrycznie wykonane nacięcia przeciwprężne eliminują naprężenia wewnętrzne (wyginanie, wybrzuszanie).
Jeżeli chodzi o tradycyjny styropian, na rynku dostępne są płyty ryflowane, na powierzchni których zostały wycięte symetryczne rowki umożliwiające odprowadzenie wilgoci (sprawdzą się w budownictwie drewnianym), a także styropian z podłużnymi nacięciami poprawiającymi sprężystość, który może być wykorzystany do izolacji termicznej dachów skośnych. Oferowane są również wyroby w różnych okładzinach, np. z folii polietylenowej w kolorze srebrnym (z przeznaczeniem do ogrzewania podłogowego) czy papy (do izolacji stropodachów płaskich). Ponadto można spotkać wyroby perforowane o zwiększonej przepuszczalności pary wodnej.
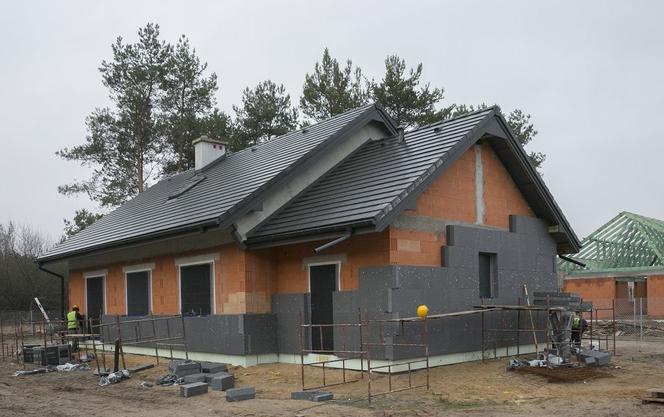
i
Materiał izolacyjny XPS
Polistyren XPS powstaje w wyniku procesu ekstruzji, w którym spieniona masa styropianowa zostaje wymieszana z określonymi dodatkami modyfikującymi i sprasowana pod ciśnieniem. Brak osłabień pomiędzy poszczególnymi komórkami powoduje większą wytrzymałość mechaniczną, odporność na ściskanie i odkształcenia oraz podnosi parametry izolacyjności termicznej, dzięki czemu XPS jest twardszy i mniej nasiąkliwy od tradycyjnego styropianu. Proces produkcji wpływa również na jego większą gęstość (20–50 kg/m³). Charakteryzuje go wysoka wytrzymałość na ściskanie przy 10-procentowym odkształceniu, która nie spada poniżej 250 kPa. Ponadto jest bardzo wytrzymały na obciążenia i nienasiąkliwy (0,5–1,5%). Z uwagi na wyjątkowo dużą odporność na wodę materiał izolacyjny XPS jest przeważnie stosowany do izolacji termicznej dachów, fundamentów i tarasów.
Płyty ekstrudowane, w zależności od użytych modyfikatorów, mają różne kolory – biały, zielony, niebieski, żółty, różowy, srebrny. Współczynnik λ wynosi 0,027–0,036 W/(mK). Płyty polistyrenu ekstrudowanego mają wymiary 120 x 60 lub 125 x 60 cm, a ich grubość wynosi od 2 do 18 cm. XPS nie jest odporny na rozpuszczalniki organiczne zawarte w niektórych klejach i masach hydroizolacyjnych. Produkuje się z niego płyty o krawędziach prostych, fazowanych, do łączenia na pióro-wpust lub na zakład. Niektóre mają szorstką albo wytłaczaną powierzchnię, aby lepiej trzymał się na nich tynk czy materiały hydroizolacyjne.
Polistyren ekstrudowany narażony jest również na szkodliwe działanie niektórych chemikaliów i promieniowania słonecznego (UV). Nie lepiej niż styropian wytrzymuje działanie ognia i wysokiej temperatury, zaczyna się bowiem topić, gdy temperatura przekroczy granicę 75°C. Jest też palny, choć dzięki substancjom dodawanym w trakcie produkcji nie podtrzymuje ognia.
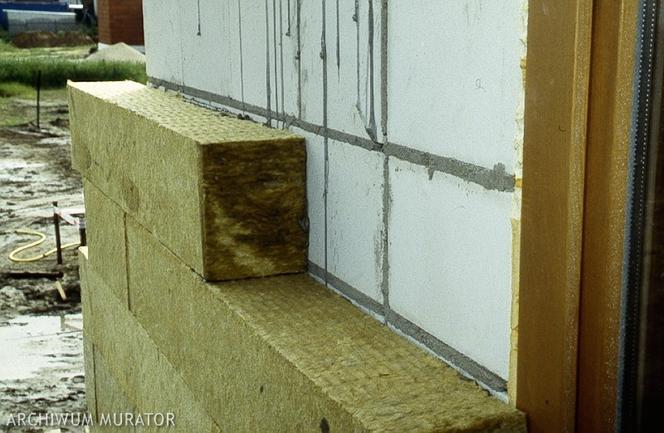
i
Materiał izolacyjny najchętniej wybierany do ocieplania poddaszy, czyli wełna mineralna
Bardzo dobre parametry i właściwości wełny mineralnej sprawiły, że stała się ona bardzo popularnym materiałem izolacyjnym i znajduje zastosowanie w wykonywaniu izolacji budowlanych i technicznych. Jeżeli chodzi o ocieplenie poddaszy (bardzo dobra sprężystość) czy ścian szkieletowych, jest najchętniej wybieranym materiałem. Wełna dostępna jest w wielu odmianach, dlatego sprawdza się przy izolacji termicznej m.in. ścian zewnętrznych czy podłóg pływających. W zależności od typu i gęstości osiąga współczynnik przewodzenia ciepła λ między 0,030 a 0,045 W/(mK). Jest trwale elastyczna, więc ruchy konstrukcji (powodowane przez obciążenie wiatrem bądź śniegiem i zmiany wilgotności materiału) nie powodują powstawania szczelin między elementami więźby a wykonaną z niej termoizolacją. Kolejną jej charakterystyczną cechą jest niepalność i ognioodporność – jest klasyfikowana jako materiał niepalny w klasach A1 lub A2, nie rozprzestrzenia ognia i topi się w bardzo wysokiej temperaturze, nie wydziela dymu. Jej włóknista struktura pochłania dźwięki i ogranicza ich przenikanie przez przegrody. Charakteryzuje się również wysoką paroprzepuszczalnością, np. przy ocieplaniu poddasza woda może swobodnie odparować (nie wnikając w materiał izolacyjny) przez szczelinę wentylacyjną albo pod deskowaniem dachu.
Polecany artykuł:
Wełna skalna
Do produkcji tego materiału termoizolacyjnego wykorzystuje się bazalt, gabro, dolomit lub kruszywo wapienne, a także materiał pochodzący z recyklingu – brykiet mineralny. Pod wpływem wysokiej temperatury surowce zostają roztopione i rozwłóknione, a następnie dodaje się do nich specjalną żywicę i formuje konkretne produkty – płyty, maty, otuliny bądź granulat. W pierwszych dwóch grupach włókna mają przeważnie układ rozproszony (lepsze właściwości mechaniczne), dostępne są również produkty, w których są one ukierunkowane prostopadle – to płyty lamelowe – a ponadto produkty łączone z papą lub laminowane welonem szklanym. W porównaniu z wełną szklaną ma ona trochę większą wytrzymałość na ściskanie, jest mniej ściśliwa, ale bardziej sprężysta. Wełna skalna sprawdzi się przy wykonywaniu izolacji termicznej ścian w metodzie ETICS, do ocieplania stropodachów niewentylowanych, fundamentów i podłóg na gruncie.
Polecany artykuł:
Wełna szklana
Ten materiał izolacyjny powstaje w podobny sposób jak wełna skalna, z tym że do jej produkcji wykorzystuje się piasek kwarcowy i stłuczkę szklaną z recyklingu. Układ włókien w matach i płytach jest ukierunkowany równolegle do powierzchni, co wymaga użycia większej ilości lepiszcza, ale poprawia wiele innych parametrów, jak np. współczynnik przewodzenia ciepła. Produkty mogą być pokryte papierem, folią aluminiową lub włókniną. Materiały izolacyjne z wełny szklanej, w porównaniu z identycznymi z wełny skalnej, są lżejsze, mniej pylą podczas cięcia, mają elastyczniejsze włókna i lepiej dostosowują się do nierówności podłoża. Z uwagi na mniejszą gęstość są zalecane do izolacji dachów skośnych, ponieważ nie obciążają nadmiernie konstrukcji. Nie powinny być stosowane w miejscach, w których byłyby poddawane dużym obciążeniom (podłogi na gruncie, tarasy). Na rynku dostępne są materiały izolacyjne, przy produkcji których nie stosuje się formaldehydu, co wpływa na poprawę jakości powietrza w pomieszczeniu. Wełna jest bardzo delikatna, przyjemna w dotyku, nie powoduje podrażnień skóry, a podczas docinania pyli znacznie mniej niż tradycyjna. Charakteryzuje się również wysoką kompresją oraz współczynnikiem λ na osiągającym nawet poziom 0,030 W/(mK).
Wełna mineralna w technologii ECOSE®
Wełna mineralna produkowana w technologii ECOSE® – innowacyjnej, wolnej od formaldehydu biotechnologii łączenia włókien, bazującej na szybko odnawialnych surowcach zamiast ropopochodnych substancjach chemicznych. Dzięki obniżonej energii skumulowanej wpływa na bardzo dobrą charakterystykę środowiskową produktu oraz przyczynia się do poprawienia stanu środowiska i rozwoju zrównoważonego w budownictwie. ECOSE® Technology została stworzona z myślą o materiałach izolacyjnych ze szklanej i kamiennej wełny mineralnej. Można ją jednak wykorzystać również w innych produktach, w których zaletą byłoby wyeliminowanie żywicy zawierającej formaldehyd.
Wełna drzewna
Do jej produkcji wykorzystuje się resztki tarcicy – długie, wąskie wióry (włókna) łączy się spoiwami mineralnymi lub poliolefinowymi i fosforanu lub siarczanu amonu, a następnie poddaje procesowi prasowania. Deklarowany współczynnik λ zależy od gęstości wyrobu, te o niższym charakteryzuje izolacyjność na poziomie 0,038–0,05 W/(mK), o wyższym zaś – 0,07–0,08 W/(mK). Wełna drzewna ma wysoką odporność na ściskanie, jest paroprzepuszczalna, nie ma tendencji do osiadania między elementami konstrukcyjnymi. Podczas jej cięcia nie powstaje gryzący pył. Ten materiał termoizolacyjny dobrze też radzi sobie z tłumieniem dźwięków uderzeniowych (krople deszczu, grad, szyszki spadające na pokrycie). Materiał ten jest palny, samogasnący (klasa odporności ogniowej E). Maty i płyty z wełny drzewnej stosuje się m.in. do ocieplania dachów skośnych lub drewnianych stropów belkowych. Można je układać między krokwiami i pod nimi, a sztywne płyty nawet na nich – jako izolację nakrokwiową.
Celuloza - materiał izolacyjny pochodzący z recyklingu
To sypki, ekologiczny materiał izolacyjny pochodzący z recyklingu – jego głównym składnikiem jest makulatura. Aby końcowy produkt charakteryzował się odpowiednimi właściwościami – jak odporność na ogień czy wilgoć – nasącza się go środkami chemicznymi (różne w zależności od producenta). Celuloza staje się materiałem niepalnym o klasie odporności na ogień B-s2,d0, nie stanowi siedliska dla insektów i gryzoni, jest odporna na powstawanie pleśni, ma również wysoką zdolność tłumienia dźwięków. Współczynnik λ wynosi od 0,037 do 0,042 W/(mK). Granulat celulozowy jest wykorzystywany do ocieplania ścian, stropów, stropodachów i poddaszy użytkowych oraz nieużytkowych. Sprawdzi się w obiektach nowych i modernizowanych. Celuloza wdmuchiwana jest maszynowo w zamknięte przestrzenie, takie jak skosy poddasza, ścianki kartonowo-gipsowe itp. (nawet bez demontażu poszczególnych warstw, co jest dodatkowym ułatwieniem). Taki montaż zapewnia szczelne wypełnienie przestrzeni materiałem i pozwala zminimalizować tworzenie się mostków termicznych. Dodatkowym atutem jest uzyskanie odpowiedniej gęstości wdmuchiwanego materiału oraz brak odpadów powstających w trakcie montażu.
Panele próżniowe
Próżniowy panel izolacyjny (VIP, ang. Vacuum Insulated Panel) zbudowany jest z dwóch elementów – materiału mikroporowatego (rdzeń) obłożonego membraną (wielowarstwowa folia). Obecnie rdzeń stanowi najczęściej krzemionka pirogeniczna w postaci proszku, charakteryzująca się m.in. niską wartością współczynnika przewodzenia ciepła i nanoporowatością (>90%). Stosuje się również: włókna szklane, otwarto komórkową piankę poliuretanową oraz polistyrenową, nanożel. Folia zapewnia ochronę przed działaniem wody i powietrza.
Próżnia nie przewodzi ciepła i jest najlepszym znanym izolatorem. λ paneli próżniowych o grubości 2–3 cm wynosi 0,007 W/(mK) i działają one podobnie jak termos. Panele próżniowe dają możliwość znacznej redukcji grubości warstwy izolacji termicznej, dlatego sprawdzą się wszędzie tam, gdzie wymagana jest dobra izolacja, a jest niewiele dostępnego miejsca na zastosowanie tradycyjnych materiałów izolacyjnych. Zalecane są jako materiały termoizolacyjne posadzek, dachów, balkonów i tarasów, wykuszy oraz jako izolacja od wewnątrz. Niestety, charakteryzuje je krótsza żywotność w porównaniu do tradycyjnych izolacji.
Montaż paneli próżniowych wymaga przeszkolonej ekipy wykonawczej, nawet najmniejsze uszkodzenie warstwy ochronnej powoduje bowiem utratę właściwości izolacyjnych. Płyt nie można poddawać żadnej obróbce mechanicznej (piłowanie, wiercenie, cięcie) – przed zamówieniem należy wykonać dokładny plan rozmieszczenia wyrobów i dokonać zakupu na wymiar. Do instalacji można używać klejów i taśm, niezawierających rozpuszczalników (np. kleje poliuretanowe, taśmy aluminiowe). Na rynku dostępne są również rozwiązania, w których panel próżniowy jest obudowany z każdej strony płytami termoizolacyjnymi PIR o wysokiej gęstości. Zapewniają one wysoki poziom ochrony przed uszkodzeniami mechanicznymi. Taka budowa gwarantuje kompatybilność z różnymi systemami hydroizolacji. Rozwiązanie to jest szczególnie zalecane do zastosowań na dachach płaskich i tarasach, gdzie dostępna przestrzeń jest znacznie ograniczona.
Płyty rezolowe (fenolowe)
To płyty termoizolacyjne z twardej piany o strukturze zamknięto komórkowej, dzięki której wyroby są praktycznie nieprzepuszczalne dla pary wodnej. Rdzeń płyt pokryty jest obustronną okładziną. W zależności od aplikacji, na której mają być stosowane, mogą być pokryte m.in. welonem szklanym (w systemach ETICS), warstwą z mikroperforacją z dodatkiem aluminium (fasady wentylowane) czy zespolone z płytami gk, gdzie dodatkowo w środku (między płytami) mają warstwę aluminiowej folii paroizolacyjnej, która blokuje przenikanie pary wodnej (ocieplenie od wewnątrz). Piana rezolowa czasem stanowi rdzeń specjalistycznych płyt termoizolacyjnych, np. może być obłożona obustronnie cienką warstwą (gr. 3 mm) styropianu grafitowego. Płyty fenolowe mają bardzo niski współczynnik λ, wynoszący 0,020–0,024 W/(mK), który gwarantuje znaczne obniżenie grubości izolatora przy wymaganej wartości współczynnika izolacyjności cieplnej U [W/(m²K)] przegrody. Mają dużą wytrzymałość na ściskanie – przy 10-procentowym odkształceniu osiąga ona 100 kPa, więc można je z powodzeniem wykorzystać jako materiały termoizolacyjne do podłóg, nawet bardzo obciążanych, np. w garażu, posadzek z ogrzewaniem podłogowym, tarasów oraz balkonów.
Aerożele
Aerożel to materiał izolacyjny o budowie komórkowej, przypominający sztywną pianę, składającą się prawie w 100% z powietrza (nanopory) oraz z żelu tworzącego jego strukturę. Te materiały izolacyjne dostępne są w formie mat, płyt i granulatu. Wynikiem specyficznej budowy są bardzo dobre właściwości izolacyjne – λd = 0,012–0,018 W/(mK). Jego gęstość objętościowa to 130–160 kg/m3, jest hydrofobowy oraz paroprzepuszczalny. Ma dobrą izolacyjność akustyczną, wysoką odporność na ogień (kl. A, trudnozapalne, niekapiące), działanie wody i wilgoci, jednak jest podatny na promieniowanie UV – dlatego jeśli stosuje się go na elewacji, powinien zostać szybko przykryty. Ocieplenie wykonuje się tak jak przy innych materiałach – na przykład tynkiem na siatce bądź okładziną elewacyjną. Mocuje się je do podłoża mechanicznie lub mechanicznie i na klej. Ten materiał izolacyjny charakteryzuje również duża elastyczność, dlatego sprawdzi się nie tylko przy izolacji termicznej płaskich powierzchni, lecz także do ocieplenia złączy budowlanych (podatnych na powstawanie mostków termicznych), takich jak ościeża okienne i drzwiowe, wnęki podokienne, płyty balkonowe czy połączenia między fundamentem a ścianą budynku.
Płyty PIR
Twarde płyty z pianki poliizocyjanurowej również mają strukturę zamknięto komórkową. Ten materiał izolacyjny jest podatny na wpływy powietrza oraz promieniowanie UV, dlatego aby płyty zachowały swoje właściwości, są pokrywane różnymi okładzinami. Może to być papier typu kraft, powłoka bitumiczna, aluminium lub włókno szklane. Dostępne są również wyroby zespolone z płytami g-k oraz paroizolacją, płytami drewnopochodnymi czy silikatowymi. Mogą mieć krawędzie proste lub typu pióro-wpust. Płyty są odporne na wilgoć i wodę, zastępują też paroizolację. Elementy z pianki PIR mają klasę palności E lub F. Wiele zależy od przeznaczenia materiałów izolacyjnych i rodzaju okładziny, w której jest umieszczona płyta. Ich współczynnik λ wynosi 0,022–0,023 W/(mK). Niska gęstość materiału – około 30 kg/m³ – sprawia, że nie obciążają one konstrukcji. Charakteryzuje je wysoka odporność na nacisk, nawet do 150 kPa/m², dlatego sprawdzą się do izolowania podłóg, tarasów i dachów płaskich. Można je ponadto stosować do wykonywania ocieplenia pod krokwiami poddaszy, nakrokwiowo – pod konstrukcją nośną pokrycia dachowego, na stropach (w tym pod podłogi ogrzewane) czy ścian zewnętrznych.
Piana poliuretanowa PUR - materiał izolacyjny do natrysku
Produkowana jest z tych samych surowców co PIR, różnica polega głównie na proporcjach poszczególnych surowców i procesie produkcyjnym. Izolacyjna piana PUR powstaje na skutek reakcji chemicznej zachodzącej po połączeniu komponentów zawierających składniki podstawowe (izocyjanian i poliol), środki spieniające oraz uniepalniacze. Oferowana jest w postaci bloków i płyt, można ją również nanosić za pomocą natrysku. Płyty są pokrywane różnymi okładzinami, np. z folii aluminiowej lub papy. Stanowią rdzeń płyt warstwowych.
Izolacja natryskowa PUR
Piany aplikuje się z podajnika, natryskując je na izolowane powierzchnie. Materiał rozpręża się i dokładnie wypełnia izolowaną przestrzeń – uzyskuje się jednorodną izolację termiczną. Na rynku dostępne są dwa rodzaje pian poliuretanowych – zamknięto- oraz otwarto komórkowa. Oba są dobrymi izolatorami, lepsze właściwości mają jednak te pierwsze. Ponadto są sztywniejsze, cięższe i wytrzymalsze.
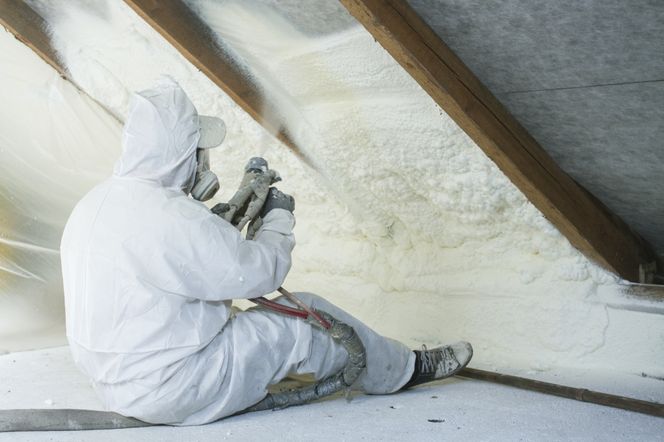
i
Mają bardzo dobry współczynnik przewodzenia ciepła – λ = 0,023–0,029 W/(mK), nie są paroprzepuszczalne, ale mają wysoką odporność na wodę. Po wyschnięciu są twarde i sztywne, zatem bardziej narażone na konsekwencje różnych naprężeń. Dzięki swojej masie oraz twardości świetnie nadają się do izolowania posadzek, fundamentów oraz płyt fundamentowych. Nanosi się je bezpośrednio na beton. Po wyschnięciu układa się kolejne warstwy podłogi, zwykle beton lub wylewkę samopoziomującą anhydrytową.
Pianka poliuretanowa otwarto komórkowa (nazywana również lekką lub półsztywną) najczęściej stosowana jest do izolacji poddaszy, stropów lekkich, ścian od strony wewnętrznej oraz zewnętrznej (metoda lekka-sucha). Swoją strukturą przypomina gąbkę, jest paroprzepuszczalna, bardzo lekka 8–10 kg/m³, a jej izolacyjność termiczna wynosi 0,036–0,040 W/(mK). Piany charakteryzują się bardzo dobrą przyczepnością do powierzchni – mogą być natryskiwane nawet na elementy metalowe.
Aby osiągnęły podawane przez producenta parametry i nie traciły ich z upływem czasu, powinny być nanoszone ściśle według instrukcji. Ważne jest ustawienie odpowiedniego ciśnienia, grubość warstwy oraz temperatura, w której wykonuje się izolację. Piany PUR mają klasę palności E lub F. Oba rodzaje pian są mało odporne na dłuższe działanie promieni UV, dlatego należy je chronić przed słońcem. W przypadku natrysku na zewnętrzne elementy konieczne będzie zabezpieczenie pianki np. farbą akrylową, bitumiczną, poliuretanową lub silikonową.
Polecany artykuł:
Maty i folie refleksyjne
Te materiały izolacyjne zbudowane są z kilku lub kilkunastu warstw otoczonych metalizowanymi okładzinami, mającymi właściwości refleksyjne – odbijające promieniowanie cieplne i jednocześnie zatrzymujące ciepło, które ucieka z pomieszczenia. Wewnętrzną warstwę najczęściej stanowi spieniona pianka polietylenowa o strukturze plastra miodu lub folia bąbelkowa (w środku zamknięte jest powietrze). Jako materiał refleksyjny stosuje się głównie folie aluminiowe pokryte jedno- lub dwustronnie przezroczystą folią poliestrową, a także pozbawione zabezpieczeń. Za główną zaletę mat uznaje się wysoki opór cieplny przy stosunkowo małej grubości materiału, a także odporność na korozję biologiczną, brak pylenia i łatwość montażu. Najlepsze właściwości refleksyjne uzyskują folie z czystego polerowanego aluminium, charakteryzujące się 98-procentowym odbiciem. Wartość współczynnika przewodzenia ciepła to 0,019–0,034 W/(mK).
Poszczególne warstwy mogą być zgrzewane termicznie, sklejone lub połączone mechanicznie. Najlepsze zabezpieczenie przed rozszczelnieniem, utlenianiem i wnikaniem wilgoci zapewnia pierwszy sposób. Folie termoizolacyjne najczęściej są wybierane do ocieplania dachów, gdyż bardzo skutecznie odbijają fale ciepła z otoczenia. Sprawdzą się również do izolacji ścian (ocieplenie od wewnątrz i od zewnątrz), podłóg oraz innych elementów konstrukcji budynku, np. ościeży okiennych. Dobrze nadają się do ocieplania skrzynek na rolety, bo są miękkie i można je dowolnie docinać.
Odpowiednie folie termoizolacyjne mogą być także stosowane przy termoizolacji kominów. Lekka warstwa izolacji nie stanowi dużego obciążenia dla konstrukcji budynku, może być także stosowana w miejscach narażonych na wilgoć, ponieważ nie absorbuje wody i hamuje osadzanie się pary wodnej. Maty wykorzystywane są często jako druga warstwa termoizolacji w układach wielowarstwowych. Zazwyczaj występują w zespole z wełną mineralną.
Szkło piankowe
Szkło piankowe otrzymywane jest z roztopionego szkła przez dodanie domieszek pianotwórczych (np. węgiel, węglan wapnia). Jest nieprzezroczyste, odporne na korozję biologiczną i chemiczną oraz niepalne (w obecności płomieni nie wydziela gazów toksycznych). Produkowane jest w dwóch odmianach:
- białe (ρob. = 240–300 kg/m³, λD = 0,038–0,042 W/(mK)) – o otwartej strukturze i podatności na nasiąkliwość,
- czarne (ρob. = 100 kg/m³, λD = 0,038 W/(mK)) – o porowatości zamkniętej, co skutkuje wysokim oporem dyfuzyjnym i brakiem nasiąkliwości.
Te materiały izolacyjne charakteryzuje bardzo dobra odporność na ściskanie – na poziomie 100–150 kPa, sztywność i brak tendencji do odkształceń nawet po wielu latach od zamontowania. Ponadto są całkowicie paroszczelne i odporne na działanie ognia (w trakcie pożaru nie wydzielają toksyn), nienasiąkliwe i odporne na chemikalia. Sprawdzą się do izolacji miejsc narażonych na duże obciążenia, np. podłóg w garażu, płyt fundamentowych czy dachów zielonych. Bloczki można wykorzystać do wymurowania pierwszej warstwy ścian, aby odizolować je termicznie od fundamentów. Na rynku dostępny jest również granulat ze spienionego szkła, powstający ze stłuczki szklanej z recyklingu, rozdzielany na frakcje. Standardowo produkowanych jest siedem różnych typów produktu – od 0,04 do 8 mm średnicy. Granulat ze spienionego szkła charakteryzują: mała gęstość, bardzo dobra odporność na ściskanie, wysoka izolacyjność termiczna i akustyczna, niepalność, a także odporność na działanie alkaliów.
Można go wykorzystywać w produkcji chemii budowlanej do poprawienia właściwości izolacyjnych wyrobów – klejów, tynków czy wylewek samopoziomujących. Na posadzce izolacyjnej można chodzić już następnego dnia. Zastosowany w tradycyjnych zaprawach murarskich zmienia ich własności i powoduje, że stają się one lekkie, ciepłochronne i likwidują mostki cieplne w ścianie.
Granulat sprawdza się jako materiał izolacyjny używany w wypełnianiu różnego rodzaju pustek. Może być stosowany luzem albo lekko związany lepiszczem cementowym lub żywicznym, również w miejscach o ograniczonej nośności (jastrych, stary strop itp.). W tradycyjnych tynkach zapewnia bardzo dobre właściwości termiczne, akustyczne i izolacyjne. Tłuczeń ze szkła piankowego to dobry materiał na podsypkę termoizolacyjną pod podłogę robioną na gruncie. Można nim również wypełnić wykopy wokół ścian fundamentowych i piwnicznych.