Jednorodzinne budownictwo prefabrykowane
Metoda prefabrykacji, czyli wytwarzania elementów składowych budowli w wytwórni i łączenie ich w całość na miejscu budowy, znacznie ułatwia i przyspiesza wznoszenie obiektu. Ponadto, co jest szczególnie ważne, uniezależnia proces budowlany od warunków pogodowych, a co za tym idzie - gwarantuje wyższą jakość wykonania.
Informacje ogólne
Kubatura domów jednorodzinnych pozwala na prefabrykację dużych elementów, nawet całych ścian z poszyciem i wypełnieniem lub bez (co ułatwia transport i montaż), stropów, więźby dachowej, a nawet dostarczanie przestrzennych segmentów scalanych na budowie w kompletny obiekt. Najpierw, zgodnie z projektem, opracowywane są szczegółowe rysunki poszczególnych elementów domu tj. paneli ściennych, stropowych i więźby dachowej. Następnie w zakładzie, przy użyciu precyzyjnych maszyn, przygotowuje się prefabrykaty. Elementy przewozi się na budowę i za pomocą dźwigu lub ręcznie montuje się na wcześniej przygotowanych fundamentach (na zdjęciu: prefabrykowany segment domu jednorodzinnego).
Fundamenty
Posadowieniem dla domu prefabrykowanego mogą być ławy i płyty żelbetowe lub fundamenty z elementów prefabrykowanych. Na życzenie klienta budynek może zostać podpiwniczony. Jeżeli do zewnętrznego wykończenia ścian stosuje się oblicówkę z cegły, przy budowie fundamentów należy przewidzieć odpowiednią odsadzkę wspierającą. Jej szerokość musi być wystarczająco duża, aby można było wykonać około 25 mm szczelinę między oblicówką a poszyciem ściany. Umożliwi to wentylację warstwy elewacyjnej i termoizolacji. Aby zapewnić właściwe zabezpieczenie drewnianego wykończenia i szkieletu przed wilgocią gruntową, ściany fundamentowe powinny wznosić się dostatecznie wysoko nad poziomem terenu wokół domu. Wysokość ta musi wynosić minimum 20 cm przy wykończeniu deskami lub tynkiem oraz minimum 15 cm przy oblicówce metalowej lub elewacji murowanej.
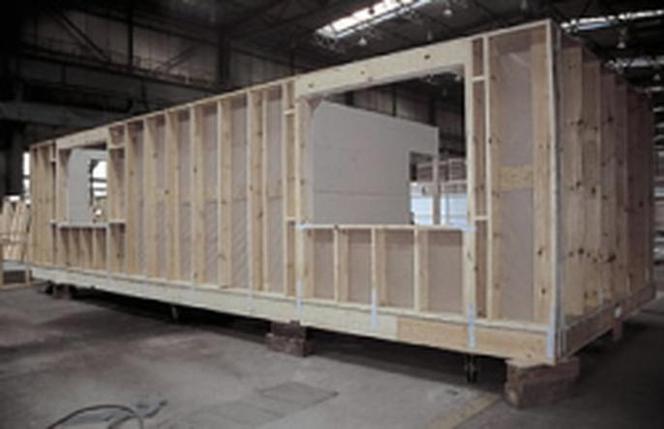
Elementy konstrukcji
Konstrukcja nośna jest charakterystyczna dla każdej z technologii prefabrykowanych domów. Przekroje poprzeczne poszczególnych elementów konstrukcyjnych i ich rozstaw osiowy dobiera się w zależności od obciążeń i przeznaczenia elementu, w którym ma być zastosowany oraz od rodzaju i gatunku materiału konstrukcyjnego. Jako poszycie i jednocześnie usztywnienie konstrukcji stosuje się płyty pilśniowe twarde, płyty OSB, płyty cementowo-wiórowe, przy czym powinny być one wodoodporne, jeśli wykorzystuje się je na zewnątrz. Do izolacji termicznej używa się wełny mineralnej lub szklanej oraz styropianu. Folie polimerowe wykorzystywane są jako paro- i wiatroizolacja Stosuje się także folie, membrany, taśmy, pianki i inne materiały hydroizolacyjne, które zabezpieczają budynek przed wilgocią. Folie i membrany wykorzystuje się do zabezpieczania ścian fundamentów, taśmy lub inne materiały w rolkach pełnią funkcję izolacji poziomej na fundamencie, natomiast pianki służą do uszczelniania połączeń konstrukcji. Konstrukcję kotwi się do fundamentu. Domy prefabrykowane są dostosowane do montowania każdego rodzaju stolarki okiennej i drzwiowej z roletami lub bez. Budynki standardowo są wentylowane grawitacyjnie ale, ponieważ są szczelne, wskazany jest również montaż wentylacji mechanicznej.
Instalacje grzewcze i sanitarne wykonuje się najczęściej z rur tworzywowych ze względu na mały ciężar i łatwość montażu. Układa się je, w osłonach lub bez, w ścianach i stropach. Instalacje elektryczne prowadzone są pod warstwą wykończeniową ścian i stropów.
Dobór materiału
Drewno. Najczęściej stosowanym materiałem jest drewno, używane w postaci naturalnej, bez substancji trudno rozkładalnych. Jest lekkie, dzięki temu wykonana konstrukcja sprawia, że koszt fundamentów jest minimalny. Mimo swej niewielkiej masy i małej akumulacji ciepła, domy drewniane charakteryzują się bardzo dobrą izolacyjnością cieplną. Należy pamiętać, że drewno jest materiałem o niejednorodnych parametrach technicznych. Wytrzymałość elementu zależy od rodzaju i gatunku drewna, ale przede wszystkim od jakości surowca. Do wad należą wszelkie nieprawidłowości w układzie włókien, które znacznie osłabiają przekrój i zmniejszają wytrzymałość. Nie bez znaczenia jest problem wilgotności. Źle wysuszone i wbudowane drewno może powodować paczenie i gnicie wykonanej z niego konstrukcji. Materiał ten wymaga więc impregnacji przeciwwilgociowej. Drewno jest materiałem łatwo palnym, ale obudowanie go płytami gipsowo-kartonowymi zabezpieczy dom przed ewentualnym pożarem. Materiał jest również podatny na szkodliwe działanie owadów, ale i tę wadę można wyeliminować, zabezpieczając drewno odpowiednimi, przeznaczonymi do tego celu, środkami chemicznymi.
Technologia przewiduje prefabrykację elementów ścian (z poszyciem, wypełnieniem i stolarką lub bez) i stropów w płyty oraz wykonanie dźwigarów dachowych w wytwórni. Prefabrykaty transportuje się na plac budowy i scala w obiekt. Budownictwo to cechuje modularny rozstaw słupków w szkielecie ścian, oraz belek stropowych i konstrukcji dachu. Przeważnie jest to 40 lub 60 cm. Podstawowe materiały używane do produkcji gotowych elementów to belki i słupy drewniane czterostronnie strugane klasy od K-21 do K-31 łączone na śruby, gwoździe i płytki kolczaste. Osie pionowe przekroju belek stropowych powinny pokrywać się z osiami pionowymi słupków. Schemat taki umożliwia prawidłowe przekazywanie obciążeń ze ścian i stropów na podwalinę, a z niej na ściany fundamentowe. Dźwigary dachowe prefabrykowane łączone są do ścian na śruby i kątowniki. Podwalina wykonana jako element konstrukcji ściany składa się z jednej lub dwóch belek. Słupy narożne ścian są wykonane z minimum 3 słupków. Jest wiele rozwiązań poszczególnych detali i połączeń elementów konstrukcji.
Parametry:
- maksymalne wymiary elementu 3/2 m,
- średni ciężar 1 m2 elementu 50-100 kg,
- podłoga parteru - grubość 30 cm; U = 0,3-0,38 [W/(m2K)],
- ściany zewnętrzne - grubość 15-25 cm, U = 0,18-0,21 [W/(m2K)],
- ściany wewnętrzne - grubość 10-25 cm,
- stropy międzykondygnacyjne - grubość 30-40 cm, U = 0,2 [W/(m2K)], rozpiętość do 6 m,
- stropodach lub dach - wiązary kratowe, rozpiętość 10-15 m, U = 0,23 [W/(m2K)],
- transport naczepami nośności min. 15 t,
- montaż za pomocą dźwigu o nośności min. 20 t,
- możliwość wybudowania 3 kondygnacji,
- czas realizacji do 3 miesięcy.
rys. 1 Przekrój przez elementy kostrukcyjne
Oznaczenia: 1 - pokrycie połaci dachówką ceramiczną, 2 - łata, 3 - kontrłata, 4 - folia wstępnegp krycia, 5 - izolacja termiczna, 6 - paroizolacja, 7 - płyta gipsowo-kartonowa, 8 - podbitka pozwalająca na wentylację dachu, 9 - warstwa wykończeniowapodłogi, 10 - sklejka lub płyta wiórowa, 11 - pustka powietrzna, 12 - ruszt z łat, 13 - oblicówka z cegły, 14 - szczelina wentylacyjna, 15 - izolacja przeciwwilgociowa, 16 - poszycie zewnętrzne, 17 - poszycie wewnętrzne, 18 - podwalina ściany, 19 - oczep stropu, 20 - nadproże, 21 - półka, 22 - zakotwienie podlicówki, 23 - podwalina impregnowana, 24 - szczelina wentylacyjna, 25 - kotew, 26 - łata fundamentowa, 27 - ibizol
Stal. Coraz większą popularność zdobywa stal i z powodzeniem może zastępować drewno. Jest materiałem o jednorodnych właściwościach. Nie jest materiałem palnym, ale wymaga zabezpieczenia przeciwpożarowego - pod wpływem wysokich temperatur (900-1300oC) może się odkształcić, zmienić cechy wytrzymałościowe. Stal musi być również zabezpieczona przed korozją. W tym celu najczęściej stosuje się powłoki galwaniczne, szczególnie jeśli są to elementy z blach cienkościennych, lub powłoki malarskie. Stal ma duży współczynnik przewodności cieplnej. Jest więc materiałem przyczyniającym się do powstawania mostków cieplnych. Dlatego elementy konstrukcji szkieletu stalowego wymagają odpowiedniego ocieplenia. Konstrukcja z profili cienkościennych jest lekka i do jej montażu nie jest potrzebny specjalistyczny sprzęt. Kształtowniki walcowane na gorąco mają większy ciężar, dlatego do transportu i montażu wykonanej z nich konstrukcji konieczny jest sprzęt ciężki. Po rozbiórce domu, stal nadaje się do ponownego wykorzystania.
Technologia przewiduje prefabrykowanie elementów ścian w panele, pełne wykonanie dźwigarów dachowych oraz przygotowanie elementów stropów międzykondygnacyjnych w wytwórni.
Konstrukcję nośną stanowią zimnogięte elementy stalowe. Profile są łączone w panele przy użyciu wkrętów samowiercących. W taki sam sposób wykonuje się dźwigary dachowe. Zabezpieczeniem antykorozyjnym jest powłoka cynkowa, a galwaniczne działanie cynku chroni również krawędzie elementów po przecięciu. Rozstaw osiowy elementów składających się na konstrukcję wynosi 60 cm. Stężenia poprzeczne ścian i rygle wykonane z taśm stalowych lub z odpowiednio przyciętych kształtowników. Ściany zewnętrzne są wykonane z ceowników i profili typu U. Ściany działowe wykonywane są również na ruszcie stalowym. Dźwigary dachowe wykonane z ceowników. Przy rozpiętościach większych niż 6 m mają węzły kryte obustronnie blachami. Wszystkie elementy są lekkie i cały montaż może być wykonany ręcznie bez użycia sprzętu ciężkiego, jeśli jest to budynek parterowy. Przy budynkach powyżej jednej kondygnacji lub przy nadbudowach konieczna jest pomoc dźwigu lub wciągarki.
Parametry:
- maksymalne wymiary elementu 3/12 m
- średni ciężar 1 m2 konstrukcji elementu około 30 kg,
- podłoga parteru - grubość 20-25 cm, U = 0,4 [W/(m2K)],
- ściany zewnętrzne - grubość 21,5 cm, U = 0,33 [W/(m2K)]; grubość 19,5 cm, U = 0,28 [W/(m2K)],
- ściany wewnętrzne - grubość 10 cm,
- strop między kondygnacjami - grubość 30 cm,
- stropodach i dach - maksymalna rozpiętość dźwigarów bez podpory pośredniej 12 m,
- transport - samochodem ciężarowym,
- możliwość wybudowania 3 kondygnacji,
- czas realizacji do 3 miesięcy.
rys. 2 Przekrój przez elementy konstrukcyjne
Oznaczenia: 1 - pokrycie połaci dachówką bitumiczną, 2 - papa podkładowa, 3 - płyta wiórowa lub sklejka, 4 - płyta dachowa z wełny szklanej GULLFIBER, 5 - szczelina wentylacyjna, 6 - termoizolacja, 7 - paroizolacja, 8 - profil sufitowy, 9 - podsufitka z płyt gipsowo-kartonowych, 10 - warstwa wykończeniowa podłogi, 11 - płyta wiórowa, 12 - wieniec stropu, 13 - izolacja wieńca, 14 - nadproże, 15 - warstwa elewacyjna-siding na stelażu metalowym, 16 - wełna szklana lub szklana, 17 - płyta wiórowa lub sklejka, 18 - wykończenie podłogi, 19 - podłoże betonowe na siatce, 20 - chudy beton, 21 - piasek ubity, 22 - bitumiczna warstwa uszczelniająca, 23 - fundament, 24 - izolacja pionowa fundamentu abizol
Beton. Beton z powodzeniem może być stosowany jako materiał konstrukcyjny w domach jednorodzinnych. Ze względu na jego ciężar (dla betonów zwykłych 1800÷2600 kg/m3) do transportu i montażu elementów konieczny jest sprzęt ciężki. Betony powyżej klasy B-15 są mrozoodporne. Problemem może być utylizacja betonu po rozbiórce domu.
Fundamenty są zbudowane w systemie słupowo-podwalinowym, z prefabrykowanych stóp, słupków dystansowych oraz układu belek podwalinowych i podłogowych. Podwaliny zewnętrzne spełniają jednocześnie funkcję ścian fundamentowych. Mają wyprofilowane półki na płyty i belki podłogowe. Podwaliny wewnętrzne stanowią podparcie pośrednie dla płyt podłogowych. Płyty podłogowe mają kształt prostokąta i stanowią wypełnienie konstrukcji podłogi. Izolacja termiczna podłogi może być układana w dwojaki sposób. Bezpośrednio na gruncie, wtedy dystans pomiędzy konstrukcją podłogi zawieszonej a izolacją termiczną tworzy pustkę powietrzną, w której można prowadzić wszystkie instalacje. Drugim sposobem jest ułożenie termoizolacji na płytach podłogowych. Technologia nie przewiduje izolacji przeciwwilgociowej, dlatego zaleca się wykonanie drenażu. Ściany zewnętrzne są wielowarstwowe. Płyta żelbetowa, będąca warstwą konstrukcyjną ściany, znajduje się na zewnątrz. Jest wzmocniona żelbetowymi żeberkami w rozstawie 60 cm znajdującymi się wewnątrz ściany. Wszystkie otwory w ścianach mają węgarki i zamontowane listwy ułatwiające montaż stolarki okiennej i drzwiowej. Ściany zewnętrzne nie wymagają tynkowania. Od wewnątrz do prefabrykatu przytwierdzone są deski stanowiące ruszt do przymocowania płyt gipsowo-kartonowych. Ściany łączy się ze sobą za pomocą kotew stalowych, a w narożach na "obce pióro".
Ściany działowe mogą być wykonane jako żelbetowe - nośne lub szkieletowe (stalowe lub drewniane). Konstrukcję stropów stanowi płyta żelbetowa i zatopione w niej co 60 cm stalowe ocynkowane kratownice. Do kratownic przymocowane są drewniane legary, do których przymocowuje się podłogę lub podsufitkę. Strop jest połączony ze ścianą na śruby stalowe w tulejach zalane betonem. Płyty stropowe można układać na dwa sposoby: albo płytą żelbetową do góry - uzyskuje się wtedy idealnie gładkie podłoże do bezpośredniego ułożenia posadzki, albo płytą żelbetową do dołu - uzyskuje się wówczas gładką powierzchnię sufitu. Zarówno w ścianach, jak i stropach pozostawione są otwory na przeprowadzenie instalacji oraz przewodów wentylacyjnych i kominowych. Zaleca się kominy prefabrykowane - ogranicza to roboty murarskie na budowie.
Wiązar dachowy stanowi kratownica drewniana prefabrykowana w wytwórni.
Parametry:
- maksymalny wymiar elementów 3/12 m,
- średni ciężar 1 m elementu 220 kg,
- podłoga parteru grubość około 15 cm; U = 0,2 [W/(m2K)],
- ściany zewnętrzne wielowarstwowe - grubość 27,2 cm; U = 0,2 [W/(m2K)],
- ściany wewnętrzne - grubość 16 cm (żelbetowe); 8-12 cm (szkielet stalowy); 7,5-10 cm (szkielet drewniany)
- strop międzykondygnacyjny - grubość około 30 cm; rozpiętość płyt do 6 m; szerokość max płyty stropowej 2,5 m,
- dach - rozpiętość dźwigarów do 15 m; U = 0,3 [W/(m2K)],
- transport - niskopodwoziowymi naczepami samochodowymi nośności min. 20 t,
- montaż - za pomocą dźwigu nośności 30-120 t,
- możliwa ilość wybudowania 6 kondygnacji,
- czas realizacji 2-3 miesiące.
rys. 3 Przekrój przez elementy konstrukcyjne
Oznaczenia: 1 - pokrycie połaci dachowej, 2 - łata, 3 - kontrłata, 4 - folia wstępnego krycia, 5 - izolacja termiczna, 6 - paroizolacja, 7 - płyta gipsowo-kartonowa, 8 - warstwa wykończeniowa podłogi, 9 - płyta wiórowa lub sklejka, 10 - ruszt drewniany, 11 - mocowanie wiązara dachowego, 12 - wieniec, 13 - nadproże z węgarkiem, 14 - kotew, 15 - płyta balkonowa, 16 - płyta żelbetowa ściany gr. 8 cm, 17 - kratownica stalowa, 18 - izolacja dźwiękochłonna, 19 - pustka powietrza, 20 - podłogowa płyta żelbetowa, 21 - podwalina w prefabrykacie, 22 - izolacja przeciwwilgociowa pozioma, 23 - belka podwalinowa, 24 - fundamentowy słupek dystansowy, 25 - stopa fundamentowa, 26 - warstwa drenażu (piasek), 27 - drenaż, 28 - szlichta, 29 - płyta podłogowa, 30 - belka podłogowa, 31 - podbicie, 32 - uszczelnienie połączeń, 33 - śruba kotwiąca strop do ściany
Stopnie prefabrykacji
Stosowane są różne stopnie prefabrykacji. W wytwórni mogą być montowane:
- elementy konstrukcji ścian, stropów i dźwigary, natomiast pozostałe prace: wstawienie okien i drzwi, montaż poszycia, izolacji oraz prace wykończeniowe i instalacyjne są wykonywane na placu budowy,
- ściany łącznie z poszyciem i rurkami na instalację elektryczną oraz konstrukcja stropów i dachu,
- gotowe elementy ścian wraz z drzwiami i oknami oraz z rurkami na instalacje, konstrukcja stropów i dachu,
- gotowe fragmenty domu - moduły wykonane w 90% w wytwórni, wyposażone w okna, drzwi, elewacje, z całkowicie zamontowanymi instalacjami wewnętrznymi.
Im więcej czynności jest przeniesionych z placu budowy pod dach fabryki, tym lepsza jest jakość domu.
Prefabrykacja niezależnie od warunków atmosferycznych, gwarantuje precyzję wykonania montażu, pełną kontrolę na poszczególnych etapach produkcji, łatwość w dokonywaniu ewentualnych zmian i poprawek. Daje też więcej czasu i lepsze warunki do montażu urządzeń, instalacji i wyposażenia. Poza tym do montażu na placu budowy wystarczą najprostsze narzędzia. Eliminujemy również przerwy technologiczne związane z wykonywaniem mokrych robót murarskich i tynkarskich. W efekcie im dalej posunięta prefabrykacja, tym większe przyspieszenie cyklu produkcyjnego. A ponieważ ograniczona jest liczba robót na placu budowy, zwiększa się ekonomiczność przedsięwzięcia.
Moduły segmentowe
Technologia przewiduje wykonanie w wytwórni gotowego fragmentu domu, wyposażonego w okna i drzwi, z wykończonymi ścianami i elewacjami oraz z zamontowanymi instalacjami wewnętrznymi. Wykonane w technologii szkieletu drewnianego z drewna czterostronnie struganego klasy k-27. Konstrukcję nośną stanowią słupki i belki w rozstawie osiowym co 60 cm połączone w panele ścienne i stropowe za pomocą gwoździ i płytek gwoździowanych a następnie w segment za pomocą śrub. Konstrukcja modułów umożliwia transport dźwigiem i łączenie podstawowych segmentów w budynek za pomocą śrub. Segment opiera się na fundamentach za pośrednictwem belki podwalinowej wykonanej z impregnowanego ciśnieniowo drewna. Jest przymocowany do podwaliny za pomocą śrub. Podłoga parteru i stropy wykonane są jako ruszt drewniany z belkami w rozstawie co 60 cm. Strop między kondygnacjami ma podwójną grubość wynikającą z zestawienia modułów. Połączenie segmentów dolnej i górnej kondygnacji wykonane za pośrednictwem podwaliny umieszczonej nad konstrukcją wieńca segmentu dolnego. Podobnie wygląda połączenie w poziomie. Stanowią je ściany sąsiadujących ze sobą segmentów stąd ich podwójna grubość. W ścianach i stropach przewidziane są otwory na przeprowadzenie instalacji, przewodów wentylacyjnych i kominowych. Schody łączące kondygnacje wykonane są również w konstrukcji drewnianej. Wiązary dachowe rozmieszczone w rozstawie osiowym 60 cm. Dźwigary drewniane prefabrykowane połączone również w segment stanowiący część poddasza. Mocowane do konstrukcji ścian na śruby i kątowniki.
Parametry:
- maksymalne wymiary modułu - 4,5(5,0)/16/3,2 m,
- średni ciężar 1 m2 segmentu 800-1000 kg,
- podłoga parteru - grubość 21 cm; U = 0,21 [W/(m2K)],
- ściany zewnętrzne - grubość 21 cm; U = 0,25 [W/(m2K)],
- ściany wewnętrzne - grubość 16,5 cm, ściana łączenia segmentów ma całkowitą grubość 33 cm,
- strop międzygondygnacyjny - całkowita grubość 60-65 cm,
- stropodach - U = 0,23 [W/(m2K)],
- transport niskopodwoziowymi naczepami samochodowymi z zawieszeniem pneumatycznym, nośności min. 20 t,
- montaż za pomocą dźwigu nośności 30-40 t,
- możliwość wybudowania 3 kondygnacji,
- czas realizacji 4-6 tygodni.
rys. 4 Przekrój przez elementy konstrukcyjne
Oznaczenia: 1 - pokrycie połaci dachu blachodachówką, 2 - łata, 3 - kontrłata, 4 - folia wstępnego krycia, 5 - termoizolacja, 6 - paroizolacja, 7 - podsufitka z płyt gipsowo-kartonowych, 8 - murłata, 9 - podbitka zapewniająca wentylację dachu, 10 - siding drewniany, 11 - ruszt aluminiowy, 12 - pustka powietrza, 13 - poszycie zewnętrzne, 14 - poszycie wewnętrzne, 15 - warstwa wykończeniowa podłogi, 16 - sklejka, 17 - płyta wiórowa, 18 - pustka powietrza, 19 - izolacja dźwiękochłonna, 20 - oczep podłogi górnego segmentu, 21 - podwalina, 22 - oczep podłogi dolnego segmentu, 23 - nadproże, 24 - tynk, 25 - styropian, 26 - podwalina, 27 - kotew, 28 - ława fundamentowa, 29 - abizol
Kontenery
Konstrukcja nośna składa się z profili stalowych zimnogiętych lub kształtowanych na gorąco, wewnętrznie i zewnętrznie zespawanych i skręconych śrubami. Konstrukcja kontenera umożliwia łączenie podstawowych segmentów w obiekty przez skręcanie w narożach za pomocą klamer stalowych lub śrub. Wszystkie elementy stalowe są zabezpieczone antykorozyjnie. Konstrukcja podłogi parteru wykonana z blachy trapezowej ocynkowanej. Ściany zewnętrzne najczęściej wykonane z płyt warstwowych. Przewidziane są trzy podstawowe typy fasad: wewnątrzleżące (warstwę elewacyjną stanowi zewnętrzne poszycie ściany, fasada jest cofnięta w stosunku do belki obwodowej stropu), zawieszane (dodatkowa płyta elewacyjna zawieszana lub mocowana na ruszcie drewnianym) i tynkowe (fasada wewnątrzleżąca dodatkowo ocieplona i pokryta tynkiem na siatce). Stropy między kondygnacjami mają podwójną grubość, wynikającą z zestawienia segmentów. Od dołu konstrukcja stropu ukryta jest pod sufitem podwieszanym. Stropodach może być wykonany jako warstwowy, z blachą trapezową na zewnątrz, z kasetami z blachy stalowej ocynkowanej i malowanej wewnątrz. Innym rozwiązaniem jest konstrukcja z podwieszonego sufitu.
Parametry:
- maksymalny wymiar modułu 12/3,6 m,
- średni ciężar modułu od 3 do 5 t,
- podłoga parteru - grubość 25 cm; U = 0,32-0,44 [W/(m2K)],
- ściany zewnętrzne - min. grubość 10 cm; k=0,2-0,43 [W/m2*K],
- ściany wewnętrzne - grubość 10-26 cm,
- strop międzykondygnacyjny - całkowita grubość 60-65 cm,
- stropodach - U = 0,23-0,28 [W/(m2K)],
- transport naczepami niskopodwoziowymi z zawieszeniem pneumatycznym o nośności min. 5 t,
- montaż - za pomocą dźwigu nośności min. 5 t,
- możliwość wybudowania 6 kondygnacji,
- czas realizacji 2-3 miesiące.
rys. 5 Przekrój przez elementy konstrukcyjne
Oznaczenia: 1 - pokrycie połaci dachowej, 2 - płyta wiórowa poszycia, 3 - wentylacja poprzeczna, 4 - belka nadająca spadek połaci, 5 - termoizolacja, 6 - belka stropowa, 7 - paroizolacja, 8 - sufit podwieszany, 9 - podsufitka z płyt gipsowo-kartonowych, 10 - wentylacja stropodachu, 11 - belka obwodowa, wieniec, 12 - zabezpieczenie ogniowe belki obwodowej, 13 - blacha podtrzymująca rynnę, 14 - płyta fasadowa, 15 - łaty drewniane, 16 - pustka powietrza, 17 - poszycie zewnętrzne, 18 - wiatroizolacja, 19 - poszycie wewnętrzne, 20 - warstwa wykończeniowa podłogi, 21 - gładź, 22 - papier, 23 - izolacja dźwiękochłonna, 24 - wylewka z chudego betonu na blachach trapezowych, 25 - kątownik do zamocowania blach trapezowych, 26 - osłona cokołu, 27 - podwalina, 28 - fundament, 29 - abizol